20hp Briggs And Stratton Ignition Coil Wiring Diagram
Introduction: Make Coiled Wire
Coiled wires (also called retractile cords) are great for keeping long wires tidy and together. Their springy nature allows them to be stretched and then return to their coiled shape, keeping your wire localized and neat looking.
Making your own coiled wires is super easy, and will work on almost any type of stranded wire with a vinyl jacket. Turn just any straight wire into a coiled one in under 10 minutes, all you need is a heat gun and a few simple tricks that I'll share to get the best results.
Ready to get coiled? Let's make!
Step 1:
Stranded wire typically has a thermoplastic vinyl jacket (common on almost every wire). It's important to use stranded wire as it's the type that is flexible, solid core wire has a single thick wire that can accept bends and will not work for this purpose.
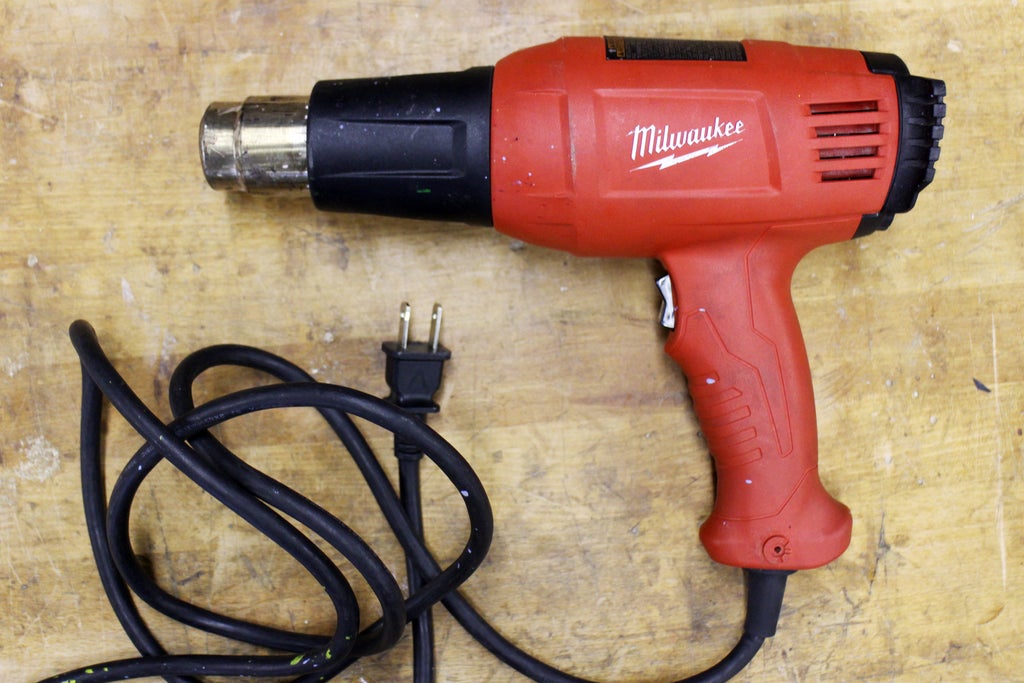
The secret to making this work is to make the vinyl wire jacket soft from heat to change shape. A heat gun is the best choice, a handheld hair dryer would also work but needs to get hot enough to allow the vinyl jacket of the wire to change shape.
Here's what you need:
- Dowel to form your coil around
- Heat gun or variable heat hair dryer
- Electric drill
- Wire cutters
- Locking pliers
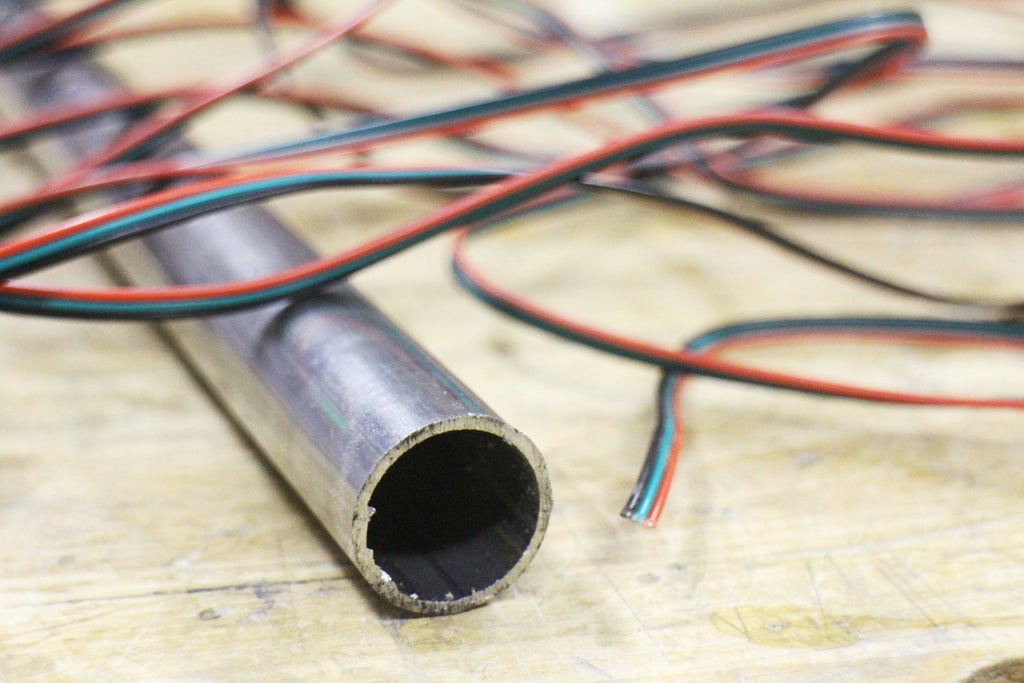
Step 2: Wrap Wire
Before wrapping the wire around the dowel, secure one end of the wire somewhere along the dowel. Since the end section of the wire can be trimmed from the coil after heating it doesn't matter how it's attached, or if the end gets damaged in any way. I used blue painter's tape as it's the first thing I grabbed.
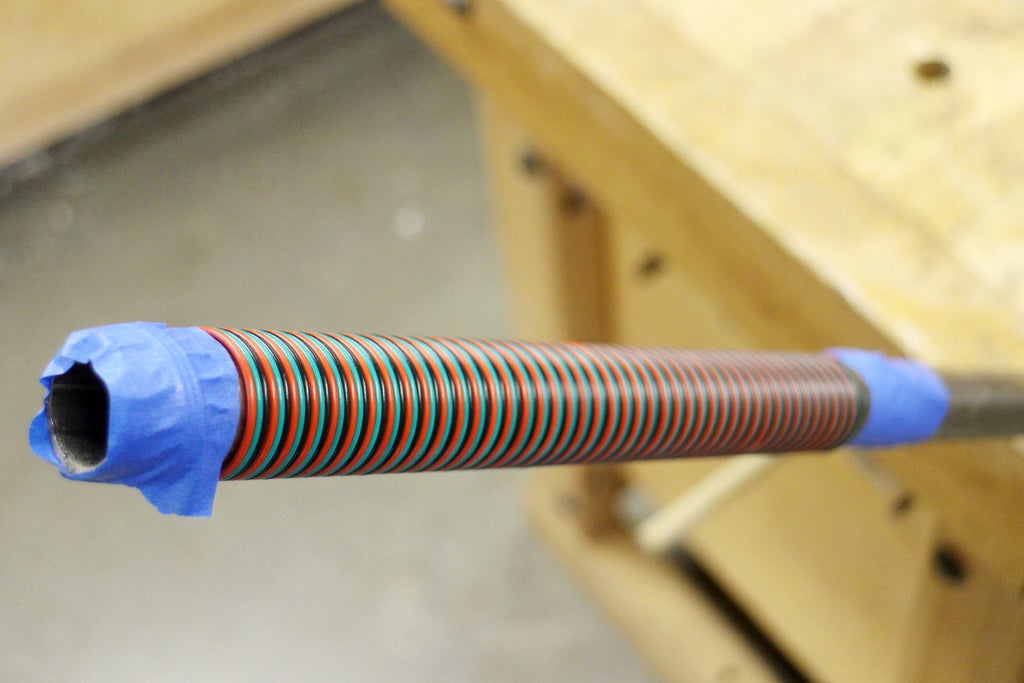
Start by wrapping from the secured end of the wire around the dowel tightly, pushing the winds together as you go. Though it doesn't matter which direction you wind the wire, I find wrapping counterclockwise easier as we'll be reverse winding the coil later using a drill and reverse winding on a drill clockwise is faster than counterclockwise.
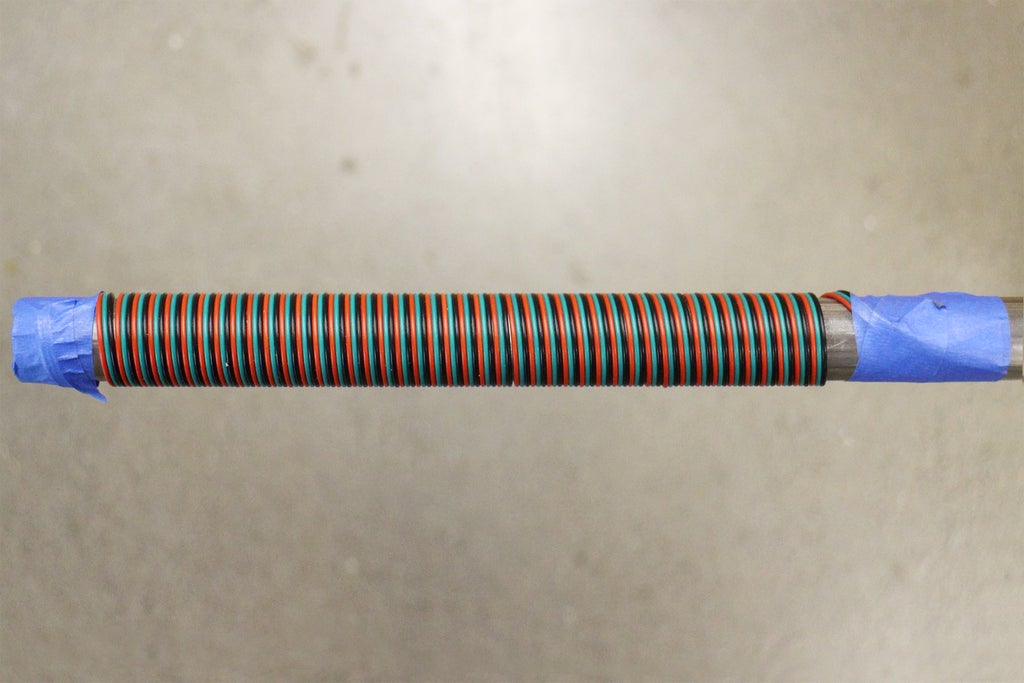
After wrapping secure the other end of the wire to the dowel to prevent unwrapping. As before, it doesn't matter if this end gets damaged from tape, heat, or clamping since we can trim it later.
Step 3: Heat
Once the wire is coiled and secured, heat the wire with the heat gun.
Since the heat output is quite strong with most heat guns it's important to heat from a safe distance and to uniformly distribute the heat through the wire by moving the gun along the dowel constantly. Allowing the heat gun to rest in any one spot too long can cause the vinyl jacket to melt.
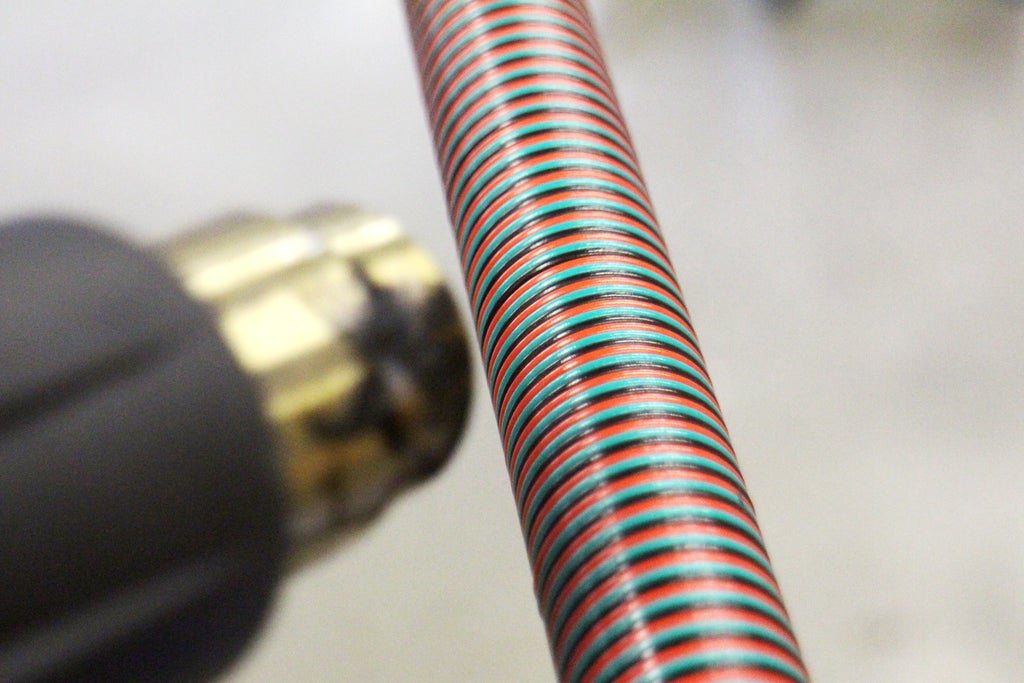
After a few minutes of heating you'll notice the vinyl jacket becoming shiny as the vinyl heats up to a critical state, altering the memory of the jacket to accept the new coil shape.
Turn off heat gun and allow the wire to cool completely before removing from the dowel.
Step 4: Remove and Examine
After the wire has cooled completely it can be removed from the dowel.
Inspect the wire for an even coil along the entire length and to see if there are any burned or melted areas from overheating. At this stage your have a coiled wire that take s up considerably less room than the same amount of wire uncoiled.
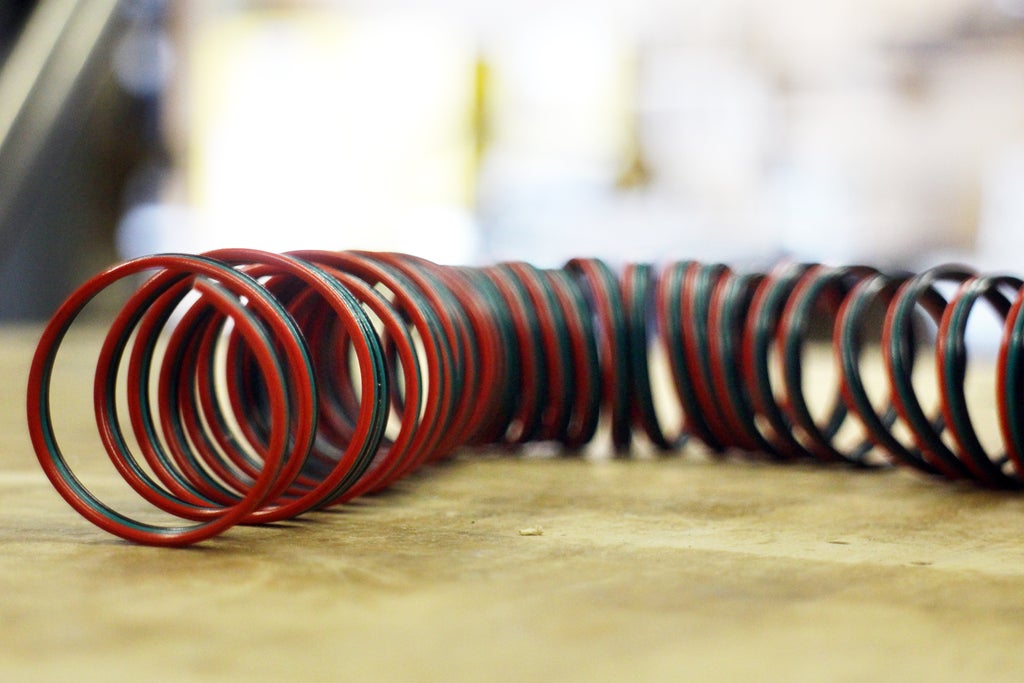
Pulling on the wire you will notice that the coil does have some memory of the shape, but lacks the 'snap' back we're accustomed to with commercial coiled wires. You can leave it as is, but there's an additional step to make this coiled wire even better.
Step 5: Reversing the Coil
By reversing the coil the spirals bind in on themselves they wire spiral becomes much more taut. We'll use a drill to help us reverse the coil, but first we need to anchor one end.
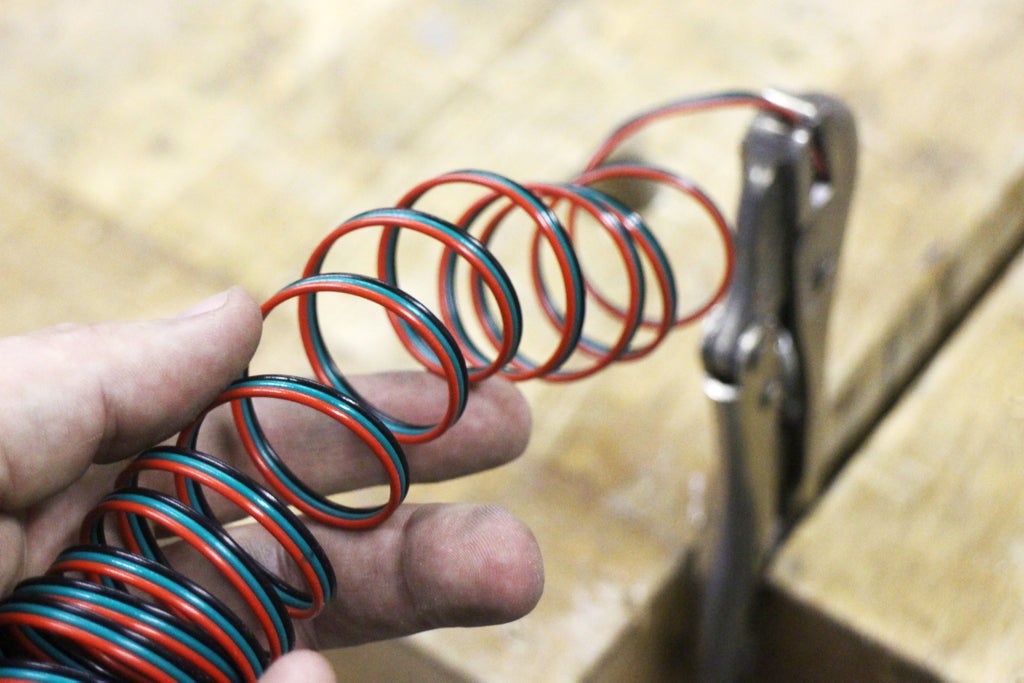
I used locking pliers to secure one end of the wire. Any damage the pliers cause to the wire can be snipped off after reversing the coil, so don't worry about the pliers crushing the jacket. Secure one end in the locking pliers and then anchor the pliers to an immovable object like your workbench or bench vise.
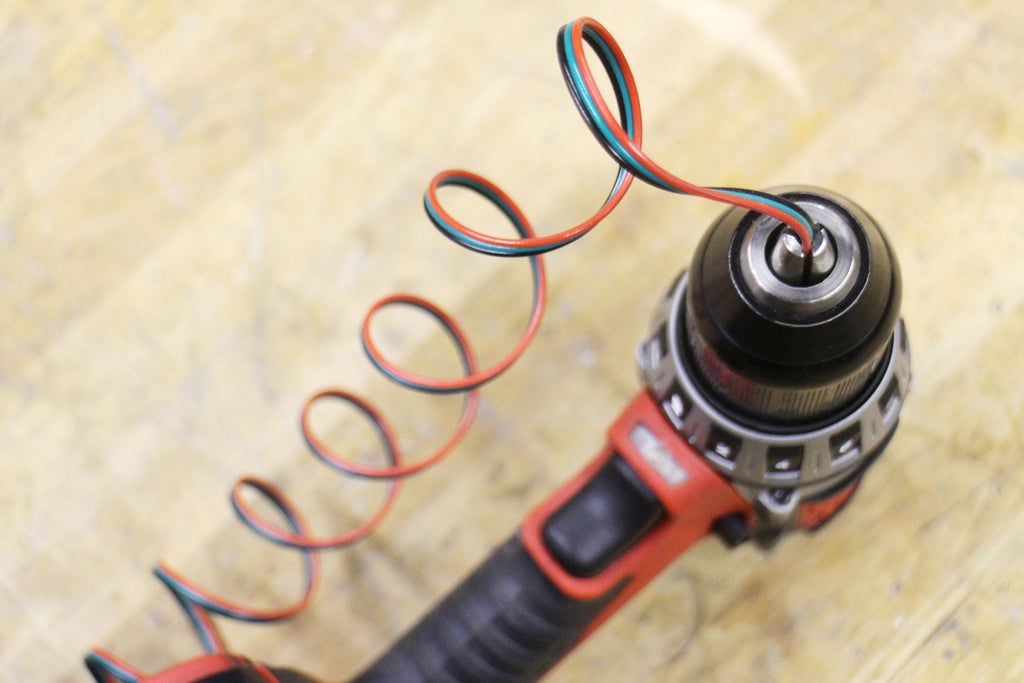
Insert the other end of the coiled wire into the jaws of the drill, then tighten the chuck to hold the wire firmly. Again, any damage the jaws cause to the wire jacket can be clipped afterwards.
Step 6: Reverse!
With both ends of the wire secured we can reverse the coil.
If your coil is clockwise then you need to have your drill going counterclockwise to reverse the coil, or vice versa depending on how you would the original coil.
Step 7: Clip Damaged Ends
After reversing the coil we can turn our attention to the damaged ends where the wire was held by the pliers or drill.
Since a crushed jacket usually means the wires inside are compromised we need to remove this small section of wire to ensure our wire has continuity. Use wire cutters to remove the section of crushed wire.
Step 8: Coiled!
With your wire now coiled it takes up much less space and is very tidy. There's really no end to the applications of coiled wire, and this technique works on all kinds of gauges for jacketed wire, from headphone cables to larger multi-strand cables (though, thicker wires will need more heat).
Stay tidy!
Have you made your own coiled wire from this Instructable? I want to see it!
Happy making :)
Be the First to Share
Recommendations
-
Anything Goes Contest 2021
Source: https://www.instructables.com/Make-Coiled-Wire/
Posted by: brodisabeoes.blogspot.com
Posting Komentar untuk "20hp Briggs And Stratton Ignition Coil Wiring Diagram"